To achieve Six Sigma, you need to improve your process performance by Minimizing the process variation, so that your process has enough room to
fluctuate within the limits of customer specifications Shifting your process average, so that it’s centered between the limits of your customer specifications
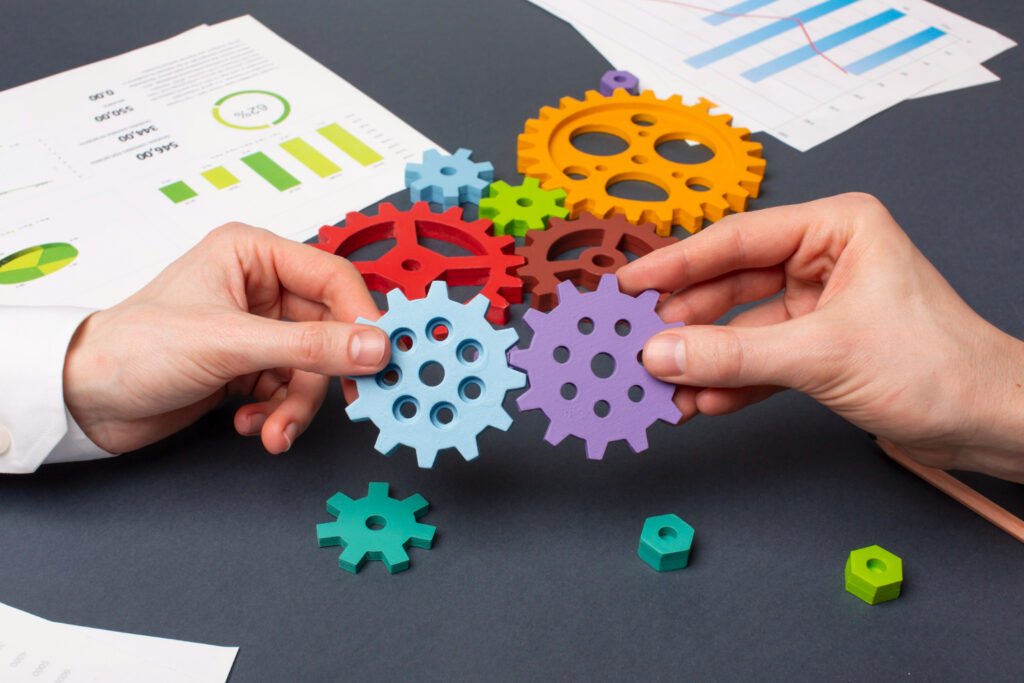
DMAIC is a systematic and rigorous methodology which can be applied to any process in order to achieve Six Sigma
It consists of 5 phases of a project:
1. Define
2. Measure
3. Analyse
4. Improve
5. Control
Six Sigma Methodology: Define Phase
Define phase is the most important aspect of any Six Sigma project. It “defines” what the project is setting out to do and scopes the effort
Goal & Objective
1. Defining the problem: The first objective of the Define phase is to clearly define the problem or opportunity for improvement that the Six Sigma project will address. This involves identifying the scope of the project, defining the goals and objectives, and establishing a project team.
2. Establishing project goals: The second objective of the Define phase is to establish specific, measurable, achievable, relevant, and time-bound (SMART) goals for the project. This involves identifying key performance indicators (KPIs) and establishing a baseline for current performance.
3. Creating a project charter: The third objective of the Define phase is to create a project charter, which is a formal document that outlines the scope of the project, the goals and objectives, the project team, the timeline, and the resources required.
4. Identifying stakeholders: The fourth objective of the Define phase is to identify all stakeholders who will be affected by the project, including customers, suppliers, employees, and management. This involves understanding their needs and expectations and ensuring that their input is considered throughout the project.
5. Establishing a business case: The fifth objective of the Define phase is to establish a business case for the project, which involves quantifying the potential benefits of the project, such as cost savings, increased revenue, or improved customer satisfaction.
Tools & Deliverables
1. Project charter: A project charter is a document that outlines the scope of the project, the goals and objectives, the project team, the timeline, and the resources required. It serves as a contract between the project team and management, ensuring that everyone is aligned and focused on the same goals.
2. Voice of the Customer (VOC): VOC is a technique for gathering and analyzing customer feedback to understand their needs, expectations, and preferences. This tool helps to identify the critical-to-quality (CTQ) characteristics of the product or service that are most important to customers.
3. Stakeholder analysis: Stakeholder analysis is a technique for identifying and understanding the needs, expectations, and perspectives of all stakeholders who will be affected by the project. This tool helps to ensure that all stakeholders are considered and their input is incorporated into the project plan.
Deliverables.
1. Problem statement: A problem statement clearly defines the problem or opportunity for improvement that the Six Sigma project will address. It includes the current state, the desired state, and the gap between them.
2. Project goals and objectives: Project goals and objectives are specific, measurable, achievable, relevant, and time-bound (SMART) targets that the Six Sigma project aims to achieve. They should be aligned with the overall goals of the organisation and address the critical-to-quality (CTQ) characteristics of the product or service.
3. Process map: A process map is a visual representation of the steps in a process, including inputs, outputs, and controls. It helps to identify waste, inefficiencies, and opportunities for improvement in the process.
4. Business case: A business case quantifies the potential benefits of the Six Sigma project, such as cost savings, increased revenue, or improved customer satisfaction. It helps to justify the investment in the project and secure support from management
- Project Charter is a contract between a project team, the
- champion and the stakeholders. It defines the what, why,
- when and by whom of the project, and includes:
- Business Case
- Problem Statement
- Project Objective and Scope
- Project Time Line
- Project Team
Stakeholder assessment for identifying gaps in stakeholder
support and develop strategies to overcome the gaps.
High-level Pareto chart
Process Maps
VOC (Voice of Customer)
VOB (Voice of Business)
CTQs (Critical to Quality Requirements
Six Sigma Methodology: Measure Phase.
The measure phase establishes the baseline performance for the process. It prioritizes potential x’s and measures x’s and Y.
Goal & Objective
1. Defining the metrics: The first objective of the Measure phase is to define the metrics that will be used to measure the performance of the process. This involves identifying the critical-to-quality (CTQ) characteristics of the product or service and selecting the appropriate metrics to measure them.
2. Establishing a baseline: The second objective of the Measure phase is to establish a baseline for the current performance of the process. This involves collecting data on the metrics and creating a process map to understand how the process works.
3. Measuring process performance: The third objective of the Measure phase is to collect data on the performance of the process using the selected metrics. This involves identifying the sources of variation in the process and measuring the extent of the variation.
4. Validating the measurement system: The fourth objective of the Measure phase is to validate the measurement system to ensure that it is accurate, reliable, and consistent. This involves conducting a gauge repeatability and reproducibility (GR&R) study to determine the measurement error and identify any sources of variation.
5. Creating a process performance baseline: The fifth objective of the Measure phase is to create a process performance baseline that can be used to compare the current performance of the process with the desired performance. This involves calculating process capability indices such as Cp and Cpk to determine how well the process is meeting the customer requirements.
- Identify all the possible x’s
- Assess the reliability of the Measurement Systems
- Validate Assumptions and Improvement Goals
- Determine COPQ (Cost of Poor Quality)
- Refine Process Understanding
- Determine Process Stability
- Determine Process Capability
Tools & Deliverables
1. Data collection plan: A data collection plan is a document that outlines the data to be collected, the data collection methods, and the sampling strategy. It helps to ensure that the data collected is accurate, relevant, and sufficient for analysis.
2. Statistical process control (SPC) charts: SPC charts are used to monitor and control the performance of a process over time. They help to identify when the process is out of control and when action needs to be taken to bring it back into control.
3. Measurement systems analysis (MSA): MSA is used to validate the measurement system and determine its accuracy, reliability, and consistency. It includes a gauge repeatability and reproducibility (GR&R) study to determine the measurement error and identify any sources of variation.
Deliverables
1. Process performance baseline: A process performance baseline is created in the Measure phase, which serves as a benchmark for future improvement efforts. It includes a calculation of process capability indices such as Cp and Cpk to determine how well the process is meeting the customer requirements.
2. Data summary report: A data summary report provides an overview of the data collected in the Measure phase. It includes a description of the data collection methods, a summary of the data collected, and any issues or challenges encountered during the data collection process.
3. Measurement system analysis report: A measurement system analysis report provides an overview of the results of the MSA conducted in the Measure phase. It includes a description of the measurement system, the results of the GR&R study, and any recommendations for improving the measurement system.
4. Control chart: A control chart is created to monitor the performance of the process over time. It includes upper and lower control limits, which help to identify when the process is out of control and when action needs to be taken to bring it back into control.
- Maps to visualize the process:
- SIPOC
- Value Steam Map
Failure Modes & Effects Analysis (FMEA) to identify and
prioritize possible process failure modes
Cause and Effect Diagram
X-Y Matrix
Statistical tools to understand more about the process data: - Basic Statistics
- Descriptive Statistics
Measurement Systems Analysis tools: - Variable and/or Attribute Gage R&R
- Gage Linearity & Accuracy or Stability
Basic Control Charts to assess process stability
Process Capability (Cpk, Ppk) & Sigma Levels
Data Collection Plan
Six Sigma Methodology: Analyze Phase
Analyze phase analyzes the relationship between process performance and the potential root causes and establishes a reliable hypothesis for improving solutions.
- It tests x-Y relationships and verifies or quantifies important x’s
Goal & Objective
1. Identifying the root causes: The first objective of the Analyze phase is to identify the root causes of the problem or issue that is affecting the process. This involves conducting a thorough analysis of the data collected in the Measure phase to identify the factors that are contributing to the variation in the process.
2. Confirming the root causes: The second objective of the Analyze phase is to confirm the root causes of the problem or issue. This involves conducting further data analysis and using tools such as cause-and-effect diagrams, process maps, and statistical analyses to validate the identified root causes.
3. Developing solutions: The third objective of the Analyze phase is to develop potential solutions to address the identified root causes. This involves brainstorming and evaluating different solutions, assessing their feasibility, and selecting the most effective solution.
4. Testing the solutions: The fourth objective of the Analyze phase is to test the selected solution to ensure that it is effective in addressing the identified root causes. This involves using statistical methods to test the solution and assessing its impact on the process performance.
5. Refining the solution: The fifth objective of the Analyze phase is to refine the solution based on the results of the testing. This involves making any necessary adjustments or modifications to the solution to ensure that it is effective and sustainable.
- Establish the Transfer Function Y = f(x)
- Validate the List of Critical x’s and Impacts
- Create a Beta Improvement Plan (e.g., pilot plan)
Tools & Deliverables
1. Fishbone diagram: A fishbone diagram, also known as a cause-and-effect diagram, is used to identify and organise the possible causes of a problem or issue. It helps to visualise the relationship between the effect and the possible causes.
2. Process maps: Process maps are used to document the steps and activities involved in the process. They help to identify where the process is breaking down and where improvements can be made.
3. Statistical analysis: Statistical analysis tools such as hypothesis testing, regression analysis, and correlation analysis are used to validate the root causes of the problem or issue and to test the effectiveness of potential solutions.
Deliverables.
1. Root cause analysis report: A root cause analysis report summarises the findings of the data analysis conducted in the Analyze phase. It identifies the root causes of the problem or issue and provides recommendations for addressing them.
2. Solution selection report: A solution selection report outlines the potential solutions that have been identified and evaluated in the Analyze phase. It provides a detailed analysis of each solution, including its feasibility, cost-effectiveness, and potential impact on the process.
3. Solution testing report: A solution testing report summarises the results of the testing conducted on the selected solution. It outlines the testing methodology, the results of the testing, and any recommendations for refining the solution.
4. Process improvement plan: A process improvement plan outlines the actions that will be taken to implement the selected solution and to improve the process. It includes a timeline for implementation, a list of responsible parties, and a plan for monitoring and evaluating the effectiveness of the solution.
Six Sigma Methodology: Improve Phase
Improve Its purpose is to identify and implement solutions to address the root causes of the problem or issue that was identified in the earlier phases.
Goal & Objective
1. Develop and evaluate potential solutions: The first objective of the Improve phase is to develop potential solutions that will address the root causes of the problem or issue. This involves brainstorming, evaluating, and selecting the best solution based on criteria such as cost, feasibility, and impact.
2. Implement the solution: The second objective is to implement the selected solution in a controlled manner. This involves developing an implementation plan, setting up a pilot project, and monitoring the solution’s performance to ensure that it is effective.
3. Verify the effectiveness of the solution: The third objective is to verify that the implemented solution has effectively addressed the root causes of the problem or issue. This involves conducting statistical analysis and other tests to determine if the solution has resulted in significant process improvement.
4. Document the improvements: The fourth objective is to document the improvements resulting from the implemented solution. This involves updating process documentation, creating new work instructions, and ensuring that the process improvements are communicated to all stakeholders.
5. Develop a control plan: The fifth objective is to develop a control plan to ensure that the process improvements are sustained over time. This involves identifying key process metrics, establishing control limits, and developing a plan for monitoring and maintaining the improved process.
The key tools and deliverables of the Improve phase include:
1. Pilot project plan: A pilot project plan outlines the steps that will be taken to implement the selected solution on a small scale. This allows the team to test the solution and make any necessary adjustments before implementing it on a larger scale.
2. Implementation plan: An implementation plan outlines the steps that will be taken to implement the selected solution on a larger scale. It includes timelines, resource allocation, and communication plans.
3. Statistical analysis: Statistical analysis tools are used to verify the effectiveness of the implemented solution and to determine if the improvements are statistically significant.
4. Control plan: A control plan outlines the steps that will be taken to ensure that the process improvements are sustained over time. It includes monitoring and measurement plans, corrective action procedures, and escalation plans.
- Statistically Proven Results from Active
- Study/Pilot
- Improvement/Implementation Plan
- Updated Stakeholder Assessment
- Revised Business Case with Return on
Investment (ROI) - Risk Assessment/Updated FMEA
- New Process Capability and Sigm
Tools & Deliverables
1. Solution implementation plan: A solution implementation plan outlines the steps that will be taken to implement the selected solution on a larger scale. It includes timelines, resource allocation, and communication plans.
2. Pilot project plan: A pilot project plan outlines the steps that will be taken to implement the selected solution on a small scale. This allows the team to test the solution and make any necessary adjustments before implementing it on a larger scale.
3. Process flow diagrams: Process flow diagrams are used to map out the process and identify areas where improvements can be made. They help to visualize the flow of materials, information, and people through the process.
4. Failure mode and effects analysis (FMEA): FMEA is used to identify potential failure modes in the process and to develop plans to prevent or mitigate them.
5. Design of experiments (DOE): DOE is used to test the effects of different process variables and to identify the optimal settings for each variable.
Deliverables
1. Solution implementation report: A solution implementation report summarises the results of the solution implementation. It identifies any issues that were encountered during implementation and provides recommendations for addressing them.
2. Final process map: A final process map documents the revised process after the implemented solution has been incorporated. It includes all the steps and activities required to carry out the process.
3. Statistical analysis report: A statistical analysis report summarises the results of the statistical analysis conducted to determine if the implemented solution has resulted in significant process improvement.
4. Process improvement report: A process improvement report summarises the improvements that have been made to the process as a result of the implemented solution. It includes a comparison of process metrics before and after the implementation of the solution.
5. Control plan: A control plan outlines the steps that will be taken to ensure that the process improvements are sustained over time. It includes monitoring and measurement plans, corrective action procedures, and escalation plans.
- Design of Experiment (DOE)
- Full Factorial
- Fractional Factorial
Pilot or Planned Study Using: - Hypothesis Testing
- Valid Measurement Systems
Implementation Plan for: - Planning
- Training
- Preparations to implement the process improvement
Six Sigma Methodology: Control Phase
Control Its purpose is to ensure that the improvements made to the process are sustained over time and that the problem or issue identified in the earlier phases does not reoccur.
Goal & Objective
The main objective of the Control phase is to establish a system for ongoing process monitoring and improvement to maintain the gains achieved during the Improve phase. The Control phase aims to:
1. Ensure that the process improvements made during the earlier phases are sustained over time and that the process remains stable.
2. Prevent the recurrence of the problem or issue identified in the Define phase by implementing a control plan that includes specific measures to detect and correct any issues that may arise.
3. Establish standard operating procedures (SOPs) to ensure consistency in the process and provide a baseline for measuring performance.
4. Provide training and education to ensure that everyone involved in the process understands the changes that have been made and their role in sustaining the improvements.
5. Use statistical process control (SPC) to monitor and control the process by tracking process performance over time.
6. Conduct process audits to ensure that the process is being followed as intended and that the improvements made are being sustained.
7. Prepare a project closure report to summarise the entire DMAIC process and to provide recommendations for future improvements or areas for further study.
- Establish mechanisms to ensure that the process sustains improved performance
- Activate a reaction or mitigation plan if the process performance is not sustained
Tools & Deliverables
1. Control charts: These are graphical representations of project data over time, which can help identify trends, patterns, and anomalies that may require further investigation.
2. Performance reports: These are regular updates on the project’s progress, which can help stakeholders understand how well the project is meeting its goals and objectives.
3. Change requests: As the project progresses, it may become necessary to make changes to the project plan or scope. Change requests can help document and track these changes, ensuring that they are properly evaluated and implemented.
4. Issue logs: These are records of any problems or issues that arise during the project, including their causes and potential solutions. They can help the project team stay on top of issues and ensure that they are resolved in a timely manner.
5. Lessons learned: Once the project is complete, it’s important to review what went well and what could have been improved. Lessons learned can help document these findings and provide insights for future projects.
Deliverables.
1. Performance reports: Regular updates on the project’s progress, which provide stakeholders with information on how the project is meeting its goals and objectives.
2. Change requests: Documentation of any changes that need to be made to the project plan or scope, including their justification, impact, and potential risks.
3. Issue logs: Records of any problems or issues that arise during the project, including their causes, potential impact, and resolution.
4. Risk management plan: A plan outlining how risks will be identified, assessed, and managed throughout the project, including contingency plans for any high-risk events.
5. Quality control plan: A plan outlining how the project’s deliverables will be reviewed, tested, and approved to ensure they meet the required quality standards.
6. Lessons learned report: A report summarising the successes, challenges, and areas for improvement from the project, which can be used to inform future projects.