Design for Six Sigma (DFSS) is a methodical technique for creating high-quality outputs by lowering the probability of flaws or errors. The DFSS process, which is based on Six Sigma, uses a number of tools and procedures to make sure that the design satisfies the needs of the client and is reliable enough to function effectively and efficiently.
Statistical analysis, simulation, and other techniques are used in DFSS to test and improve the design with the goal of identifying and removing any issues before they arise. This makes it more likely that the finished product or process will not only be free of flaws but will also satisfy the requirements of the client.
A cross-functional team of designers, engineers, and quality specialists collaborate to design and test the product or process when DFSS is often employed in the early stages of product or process development. Identifying customer needs and requirements, building a thorough design plan, making and testing prototypes, and verifying the final design are some of the main components of DFSS.
DFSS is an effective instrument for guaranteeing that goods and operations are created to the highest levels of quality and client satisfaction, resulting in increased profitability and market success.
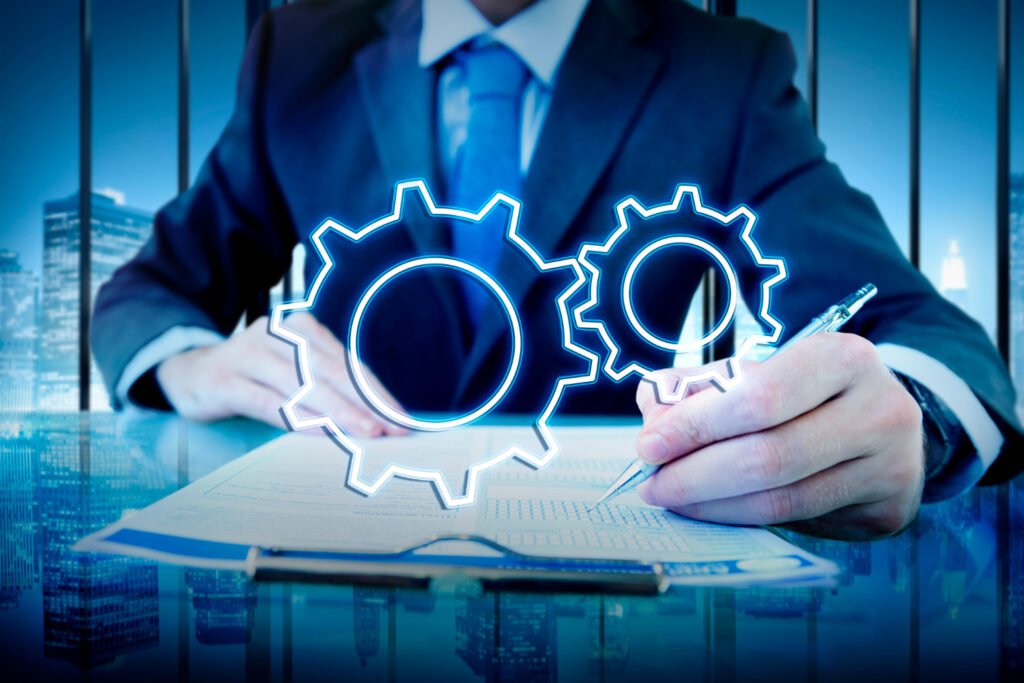
The Five Phases of DFSS
1. Define
Determining the customer’s needs is the first step in the DFSS process. Finding out what the customer values most in a product or service entails doing this. Market analysis, surveys, and focus groups are frequently used to determine client requirements. Following the definition of the requirements, they are converted into quantifiable traits that may be utilized to direct the design process.
2. Measure
The present process capability is measured in the second stage of the DFSS. To assess the performance of the current product or service, data must be gathered. Statistical process control (SPC) techniques, such as control charts and process capability analysis, are generally used to gather the data.
3. Analyze
The analysis of the data to find areas for improvement is the third stage of DFSS. Regression analysis and design of experiments (DOE) are two statistical approaches that can be used to determine the variables that have the biggest impact on a product’s or service’s performance. Finding the critical-to-quality (CTQ) traits that must be under control in order to satisfy the needs of the client is the aim of this phase.
4. Design
Designing a new procedure that complies with client requirements is the fourth stage of the DFSS. In this stage, a design that maximizes the functionality of the good or service is created using the data obtained in the other stages. Typically, computer-aided design (CAD) software is used to create the design
5. Verify
Verifying the effectiveness and sustainability of the solutions created in the previous phase is the final step. This entails putting the solutions into practice, keeping an eye on the outcomes, and making any necessary modifications to make sure the performance goals are achieved.
Benefits of DFSS
There are several benefits to implementing DFSS, including
1. Improved customer satisfaction
2. Reduced defects and variability
3. Lower costs
4. Competitive advantage
Drawbacks of DFSS
DFSS has many benefits, but there are also some drawbacks to consider:
1. Time-consuming:- DFSS can be a time-consuming process, especially for complex products or processes.
2. High level of expertise required:- DFSS requires a high level of expertise in Six Sigma methodology and statistical analysis.
3. Costly:- DFSS can be costly to implement, especially if the company needs to invest in specialized tools or software.
Key Differences Between DFSS and DMAIC
DFSS Methodology
- Define
- Measure
- Analyze
- Design
- Verify
DMAIC Methodology
- Define
- Measure
- Analyze
- Improve
- Control
Key Differences Between DFSS and DMAIC
- Focus
- Scope
- Tools and Techniques
- Data Collection
- Timeframe
- Risks and Opportunities